Frequently Asked Questions
What are common issues encountered in pressure vessel design?
When designing a nice pressure vessel, it is necessary to select an appropriate design pressure based on the pressure the vessel will withstand. An excessively high design pressure may cause material failure, while an excessively low design pressure may not meet usage requirements.
There are many common issues encountered in pressure vessel design. Here are some of the most frequent ones:
1.Selection of Vessel Shape: The appropriate vessel shape must be chosen during design. Common shapes include cylindrical, spherical, and ellipsoidal vessels, each affecting pressure resistance and stress distribution differently.
2.Selection of Design Pressure: When designing pressure vessels, it is essential to choose an appropriate design pressure based on the pressure the vessel will withstand. An excessively high design pressure may lead to material failure, while an insufficient design pressure may fail to meet operational requirements.
3.Material Selection: Choosing the right material for pressure vessels is crucial to ensure they can withstand the required pressure. Common materials include carbon steel, stainless steel, and alloy steel, each with different strength and corrosion resistance properties. The selection should be based on specific application requirements.
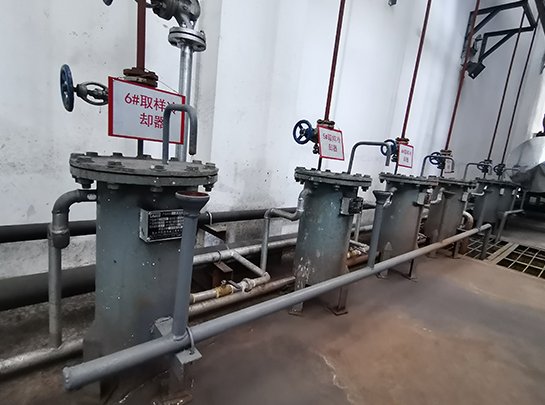
4.Wall Thickness Calculation: When designing a pressure vessel, it is essential to calculate the appropriate wall thickness. If the wall is too thin, the vessel may rupture, while an excessively thick wall increases manufacturing costs. The calculation must consider factors such as the pressure the vessel will withstand, the strength of the material, and the vessel’s dimensions.
5. Welding and Connection Design: Welding and connection design are critical in pressure vessel design. They significantly impact the vessel’s strength and sealing performance. Attention must be paid to the strength of the welds and the reliability of the connecting components.
6. Stress Analysis: Stress analysis is an important part of pressure vessel design. It helps engineers understand the stress distribution within the vessel, allowing them to determine appropriate design parameters and material selection to ensure safety and reliability.
7. Safety Valve Design: The design of safety valves must be considered in pressure vessel design. Safety valves automatically release pressure when it exceeds the design limit, preventing vessel failure. The selection and design of safety valves should account for the vessel’s pressure range and operating conditions.
8. Material Fatigue and Creep: Material fatigue and creep properties must be taken into account in pressure vessel design. Fatigue and creep refer to the deformation and failure of materials under prolonged stress. Proper material selection and design parameters are necessary to prevent these issues.
9. Sealing Design: The sealing performance of a pressure vessel is crucial to preventing leaks and meeting customer requirements. Proper sealing materials and structures must be chosen to ensure effective sealing.
10. Manufacturing and Inspection: After designing a pressure vessel, the manufacturing and inspection processes must be conducted. Manufacturing should adhere to process specifications and quality control standards, while inspection must comply with relevant regulations to ensure the vessel’s quality and safety.
What are the main applications of pressure vessel forgings?
Nice pressure vessels are mainly used in chemical containers, such as tubular heat exchangers, pressure vessels, boilers, condensers, central air conditioning systems, evaporators, and seawater desalination. Metal materials not only have high rigidity but also excellent thermal conductivity.
In the calculation of fixed pressure vessel forgings, the axial stress of the shell is determined based on various working conditions related to temperature differences. When either the axial stress of the heat exchange tubes or the pull-off force between the heat exchange tubes and the tube sheet fails to meet strength (or stability) requirements, an expansion joint must be installed.
In the strength calibration calculation of fixed pressure vessels, if the vessel’s thickness is determined without an expansion joint, its strength may sometimes be insufficient. After adding an expansion joint, the thickness of the tube sheet may meet the requirements. In such cases, an expansion joint can also be used to reduce the thickness of the tube sheet, but a comprehensive evaluation of material consumption, manufacturing difficulty, safety, and economic efficiency must be conducted.
With the increasing size of chemical equipment and power plants, the diameters of pressure vessel forgings are becoming larger, with diameters of 4m-5m being quite common. The characteristics of large pressure vessel forgings include a high number of tube holes, low hole density, deep hole depth, and high precision and surface finish requirements.
Pressure vessel forgings are widely used in industries such as shell-and-tube heat exchangers, boilers, pressure vessels, steam turbines, and large central air conditioning systems.
Nice pressure vessels are mainly used in chemical containers, such as shell-and-tube heat exchangers, pressure vessels, boilers, condensers, central air conditioners, evaporators, and seawater desalination systems. Metal materials not only have high rigidity but also excellent thermal conductivity.
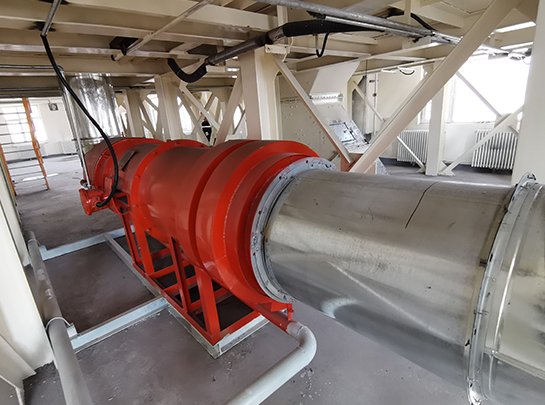
Depending on the operating environment, different materials are used. Generally, Q345R vessel plates are commonly used. For primary and secondary pressure vessels without circulating corrosive media, carbon steel composite plates can be used. In environments with strong acids, high pressure, high temperatures, or nuclear energy, corrosion-resistant materials such as stainless steel, 16Mn, and titanium alloys are required. The application of new synthetic materials has brought new vitality to tube sheet products.
The tube sheets of the four types of pressure vessels require relatively high precision. Traditionally, hole machining was performed using manual marking and radial drilling. With the increasing size of chemical containers, the diameter of tube sheets has also increased, and their thickness has gradually increased. CNC technology has been introduced for tube sheet machining, typically using CNC drilling machines for pilot holes, followed by radial drilling. Some large enterprises have also gradually adopted machining centers for efficient and high-precision hole processing. The demand for large, thick tube sheets is increasing, particularly in the fields of nuclear power, seawater desalination, and central air conditioning heat exchangers.
During the inspection of pressure vessels, the main indicators include hole position, hole diameter tolerance, hole surface finish, burrs, and slot positioning. For double tube sheets, the alignment of hole positions between the two sheets is crucial. CNC drilling machines are generally used to ensure accuracy. Compared with thick plates, the verticality of holes over 300mm is particularly important. These large-diameter thick plates require precision tools and equipment, and the application of special gantry machining centers is becoming increasingly common.
What are the inspection methods for pressure vessels?
The internal and external inspection of Nice pressure vessels must be conducted after shutdown and cleaning of the vessel. The specific inspection scope includes not only the contents of the external inspection but also the corrosion and damage on both internal and external surfaces. Visual inspection and high-magnification examination shall be used to check welds, inspect the stainless steel sealing connection areas and stress points for cracks, and, if necessary, ultrasonic or radiographic testing shall be performed to assess the weld quality. Wall thickness measurements shall also be taken.
There are many methods for inspecting Baotou pressure vessels, including external inspection, internal and external inspection, and examination.
1. External Inspection: Also known as operational inspection. The specific inspection content includes checking whether the outer surface of the pressure vessel has cracks, deformation, leakage, localized overheating, or other abnormalities; whether the accessories are complete and functional; whether the anchor bolts are intact and properly tightened; and whether there are any abnormal conditions such as sinking, tilting, or damage to the anti-corrosion coating. External inspection is not only the responsibility of inspection personnel but also a routine task for operational personnel during regular patrol inspections. If serious hazards are found (such as cracks, deformation, or severe leakage in stress-bearing components), operation should be stopped, and relevant personnel should be notified.
2. Internal and External Inspection: The internal and external inspection of Baotou pressure vessels must be conducted after shutdown and vessel cleaning. The inspection content includes not only all aspects of external inspection but also checking for corrosion and damage on the internal and external surfaces; visually and with a high-magnification magnifying glass, inspecting weld seams, stainless steel sealing connection areas, and stress locations for cracks. If necessary, ultrasonic or radiographic testing should be used to inspect weld quality. Wall thickness measurements should be conducted, and if the measured thickness is below the vessel’s design thickness, a strength reassessment should be performed to determine whether pressure reduction or maintenance measures are needed. For vessels where alloy composition changes may occur, metallographic analysis and examination should be conducted. For high-pressure and ultra-high-pressure vessels, key anchor bolts should be checked for cracks using magnetic particle inspection or dye penetrant testing.
Based on the results of the internal and external inspection, defects should be analyzed, and a resolution plan should be determined. After maintenance, re-inspection must be performed. Internal and external inspections of pressure vessel bolts should be conducted every three years, but for vessels containing toxic substances, the inspection cycle should be shortened. If serious defects in the vessel or weld quality are found during operation, or if the corrosion resistance of the material is uncertain, the inspection cycle should also be shortened.
Inspection:
In addition to new inspection items, pressure vessel inspections should include a communication pressure test. Non-destructive testing (NDT) and sampling inspection or welding inspection should be conducted on critical welds. However, for vessels with low working pressure, non-flammable, non-toxic, and non-corrosive media, if no defects are found and operational experience has been gained, NDT and inspections may not be required.
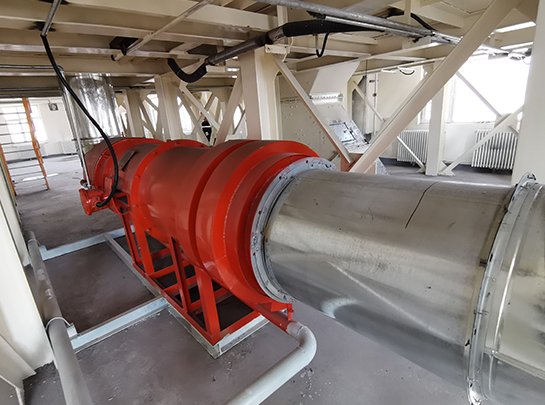
The inspection cycle for vessels is typically at least once every six years. Once operational experience is gained and one or two internal and external inspections confirm corrosion resistance, the vessel can be considered compliant with standards.